How do I choose the right ISO Certification?
Choosing the right ISO certification for your organisation involves several considerations to ensure that the certification aligns with your business objectives and adds value beyond mere compliance. Here are some key factors to consider:
Organisational Objectives: Before selecting an ISO Certification, it’s crucial to have clear objectives and goals that you aim to achieve through the certification.
Awareness about ISO Standards: Understand the various ISO Certification Standards available and determine which one aligns with your business processes and goals.
Scope of the Certification: Define the scope of the certification, considering the areas of your business you want to be ISO certified.
Cost of Implementation: Evaluate the financial implications, including the cost of implementation and maintenance of the ISO standards within your organisation.
Changes to Business Management System: Consider the changes required to your current business management system to meet the ISO standards.
Reputation of the Certification Body: Choose a certification body with a solid reputation, as this can impact the credibility and recognition of your certification.
Accreditation: Ensure the certification body is accredited, as accreditation provides independent confirmation of competence. However, non-accreditation does not necessarily mean the certification body is not reputable.
Experience in Your Field: Check if the certification body has experience with the specific ISO standard you’re seeking and in your industry
Value Addition: Consider a certification body that can bring additional value to the relationship, not just a certificate.
Remember, certification is a commitment to continuous improvement and should be viewed as an investment in your organization’s future. It’s advisable to conduct thorough research and possibly consult with experts in the field to make an informed decision.
What is an ISO certification project?
An ISO certification project is a structured process that a company undertakes to obtain a certification for its management system as per one of the International Organisation for Standardisation (ISO) standards. These standards are designed to help organizations manage business risks and meet specific objectives. There are over 80 management system standards, each supporting different goals.
The project typically involves several key steps:
Preparation: This includes training, conducting gap analyses, and planning.
Documentation: Developing custom procedures and writing required documentation based on the company’s context.
Implementation: Introducing new procedures to employees and integrating them into the work processes.
Internal Audit: Conducting self-inspections to ensure the effective implementation of the ISO system.
Certification: Undergoing a certification audit by an independent, accredited registrar.
The aim is not just to achieve certification but also to improve business operations and ensure long-term success and sustainability. The process should be tailored to fit the company’s unique needs, making business processes leaner and more efficient.
Are there any industry-specific ISO standards?
Yes, there are several industry-specific ISO standards designed to address the unique requirements of various sectors. Here are some examples:
ISO 13485: This standard is specific to medical devices and outlines requirements for a quality management system where an organisation needs to demonstrate its ability to provide medical devices and related services that consistently meet customer and applicable regulatory requirements.
ISO 22163: It applies to the railway industry for quality management systems and specifies requirements for organisations in this sector.
ISO 22000: This standard focuses on food safety management and helps organisations identify and control food safety hazards
ISO 27001: It is designed for information security management and helps organisations keep information assets secure
ISO 45001: This standard provides guidelines for an occupational health and safety (OH&S) management system to help organisations improve employee safety, reduce workplace risks, and create better, safer working conditions.
These standards are part of a larger collection that cater to specific industries, ensuring that the standards are relevant and can effectively improve quality, safety, and efficiency within those fields.
How can I choose the right standard for my industry?
Choosing the right ISO standard for your industry involves a few key considerations to ensure that the standard aligns with your business objectives and industry requirements. Here are some steps to guide you through the process:
Identify Your Organisational Objectives: Determine what goals you want to achieve through ISO certification. This could be improving product quality, enhancing customer satisfaction, or streamlining processes.
Understand the ISO Standards: Gain a basic understanding of the different ISO standards available. For example, ISO 9001 is for quality management, while ISO 27001 focuses on information security1
Determine the Scope of Certification: Consider the extent to which the ISO standard will apply to your operations. It should cover the key areas of your business that you wish to standardize and improve.
Evaluate the Cost of Implementation: Assess the financial investment required for implementing the ISO standard, including training, documentation, and the certification process itself.
Consider Your Industry: Some ISO standards are tailored to specific industries. For instance, ISO 13485 is for medical devices, and ISO 22000 is for food safety management. Choose a standard that is relevant to your industry.
Consult with Stakeholders: Engage with employees, customers, and other stakeholders to understand their needs and expectations from the ISO certification.
Research Certification Bodies: Look for an accredited certification body with experience in your industry and a good reputation among potential clients.
By following these steps, you can select an ISO standard that not only meets the regulatory and customer requirements but also drives continuous improvement and adds value to your business. Remember, the right ISO standard should help your organisation achieve its strategic goals and enhance overall performance.
What are the common challenges in ISO Implementation?
Implementing ISO standards can be a complex process, and organisations often face several common challenges. Here are some of the most frequently encountered issues:
Lack of Management Support: Successful ISO implementation requires strong leadership and commitment from top management. Without it, allocating resources and driving necessary changes can be difficult.
Resistance to Change: Employees may resist changes to long-established practices due to concerns about job security or task stability
Complex Documentation Requirements: ISO standards often require comprehensive documentation, which can be time-consuming and challenging to maintain.
Resource Constraints: Limited funding, time, and expertise can hinder the effective implementation of ISO standards.
Maintaining Continuous Improvement: After achieving certification, organisations might struggle to continue improving processes and maintaining high standards.
What are some best practices for overcoming resistance to change?
Overcoming resistance to change in an organisation involves a combination of strategic planning, communication, and support. Here are some best practices to help manage and mitigate resistance:
Transparent Communication: Clearly communicate the reasons for the change, the benefits it will bring, and how it will be implemented. Transparency helps build trust and reduces uncertainty.
Inclusive Decision-Making: Involve employees in the change process. When people feel they have a say in the changes, they are more likely to support and adopt them.
Empathy and Support: Understand the concerns and emotions of those affected by the change. Offer support and address their fears and objections.
Training and Education: Provide training and resources to help employees develop the skills needed to adapt to the change. This reduces anxiety about new responsibilities or processes.
Leadership Alignment: Ensure that leaders at all levels are aligned with the change and are actively supporting it. Leadership plays a crucial role in setting the tone for change acceptance.
Quick Wins: Identify and celebrate early successes related to the change. This can build momentum and show the positive impact of the change.
Identify and Address Root Causes: Instead of just dealing with the symptoms of resistance, identify the underlying reasons why employees resist and address those issues.
Structured Change Management Approach: Use a structured approach to manage the change process, from initiation to implementation, to ensure consistency and clarity
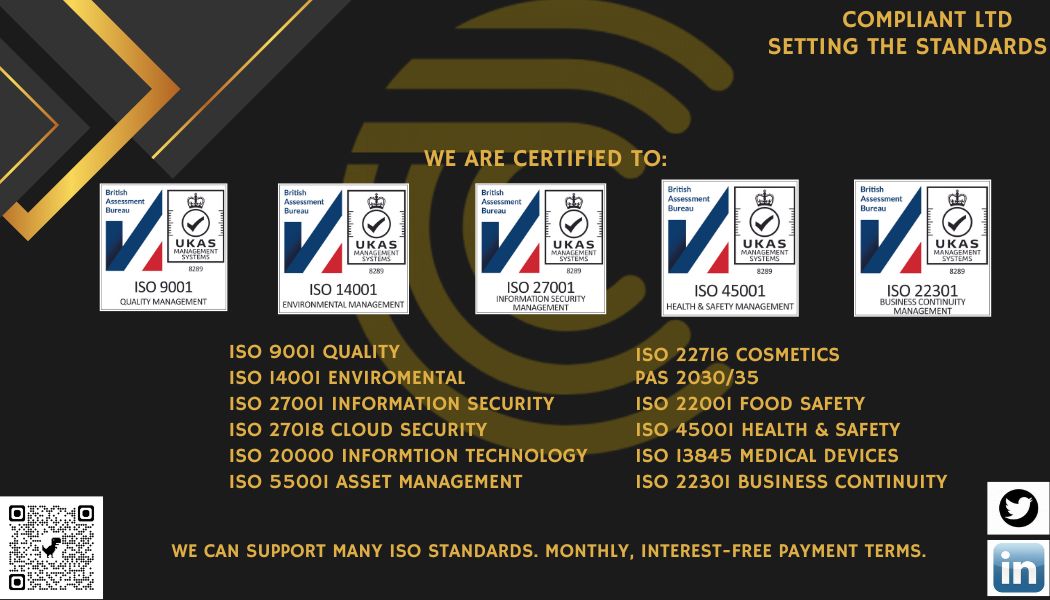
Recent Comments